Manufacturing Execution System
With experience in electronics manufacturing based on the Japanese methodology of Kanban and JIT production, MQuest has developed the AUTOMOUNT MACHINE MANAGEMENT SYSTEM (AMMS) for the electronics PCBA industry. The system has helped global manufacturers like Sony, Panasonic, and Philips manufacture their PCB boards. Major PCBA vendors in Asia have also relied on the technology to meet the high mix, low volume production requirements prevalent today. The system has built in intelligence to learn and adapt the manufacturing parameters with actual production data.
AMMS is a powerful real time management system for the electronics manufacturing operation. It gives a strong advantage with online information, real time accuracy, transparency and flexibility of operation over the competitors.
The Auto Mount Management System (AMMS) was developed for the electronics PCBA industry, based on many years of experience in electronics manufacturing using Japanese methodology of Kanban and JIT production.
The system has helped global manufacturers like Sony, Panasonic and Philips. Major PCBA contractors in Asia have also relied on the technology to meet the high mix, low volume production requirements prevalent today. The system has built in intelligence to learn and adapt the manufacturing parameters with actual production data.
AMMS is a powerful real time management system for the electronics manufacturing operation. It gives a strong advantage with online information, real time accuracy, transparency and flexibility of operation over the competitors.
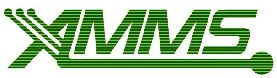
The AMMS software suite of programs manages the production floor right from production planning, material control to machine monitoring. It features Production Scheduling, Parts Control, Machine Monitoring and Production Planning as the core modules.
Structured to adapt to the traditional line and cell concept of equipment on the production floor, the system supports multiple equipment lines utilizing numerous placement machines from various OEM vendors.
Maximizes equipment utilization, tracking and traceability, improves process throughput, reduces defects, scrap and rework of boards and procurement of excess materials.
Benefits of AMMS

Increases Production Planning Efficiency

Increases Productivity and Quality

Decreases Manpower Cost

Decreases Material and Preparation Cost
This system has four major operations such as

Parts control System
We also design and provide immigration gates that give maximum convenience and security. These automated gates are used to verify the passport holder’s identity by biometric and face recognition which are taken at the time of entry.Â
Advanced Production Scheduler
The Advanced Production Scheduler enables production planner to accurately allocate jobs to the production lines easily. With the actual production status of each production lines visible at the click of a mouse, planners will be able to optimize every resource, and thereby reducing idling time. At the same time, it will now be possible to inform customers of the delivery date almost instantly and with confidence of accuracy.

Benefits

Production schedule and capacity reports

Efficient job allocation method to maximize machine time

Manufacturing lead time reduction

Real time production status feedback

Easy drag and drop planning with high planning accuracy

Optimize throughput and production planning

Flexible job adjustments

1 day lot production

Accuracy of schedule planning

Visible schedule display
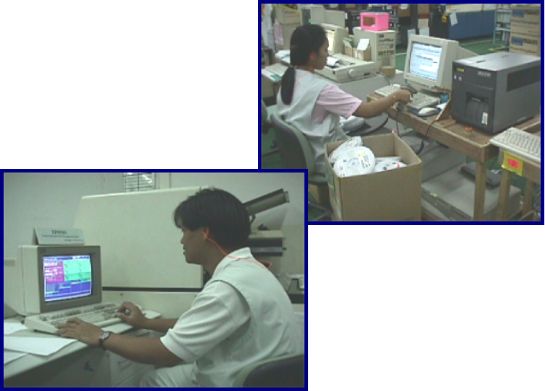
Material / Parts Control
With material control, the manufacturers are able to track and trace every single component used during manufacturing. It will be able to locate every single reel of component in the manufacturing floor and also linked to the production lot it has been used on.
When receiving parts from suppliers, each reel is uniquely tracked. This allow a full visibility of the parts origin.
Benefits

Reduce part searching time to maximize productivity

Reduce excess material on the production floor

Real time inventory, possible to achieve at least 98% accuracy

Advance alert of parts exhaust to reduce machine down time

Able to forecast and recommend safety stock to minimize line material shortage

Parts traceability

Machine Monitoring
Machine Monitoring help production improve quality and machine utilization rate. The early part exhaust warning system set alert timing so that parts can be prepared before part exhaust. This ensure that production information are collected from each machine. Maintenance can be planned as each parts on the machine is tracked. Tool life can be tracked via running hours, or the number of parts placed.
Benefits

Real time machine communication

Standard procedure for model change and part exhaust

Eliminate parts mis mount

Accurate job finish time

Early part exhaust warning

Detailed machine stop history

Detailed pickup error history

Tool life usage monitoring
Production / Monitoring Control
Production Management module enables the management team to have an overview of the entire manufacturing plant with the click of a mouse. Productivity information are consolidate and displayed in real time. Detailed information of each process can be monitored by drilling down. Information is available online and therefore, managers can also viewed them over the internet.
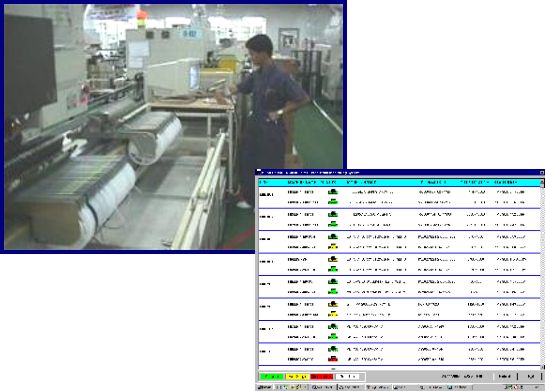
Benefits

Online monitoring of total SMT production facilities by production lines and machines

Simple drill down to view detailed machine performance and job status

Can be viewed from remote site, facilitates multi plant and subcon operation

Consolidated capacity and machine availability information

Graphical display and ease of use
Manufacturing The Need For AMMS
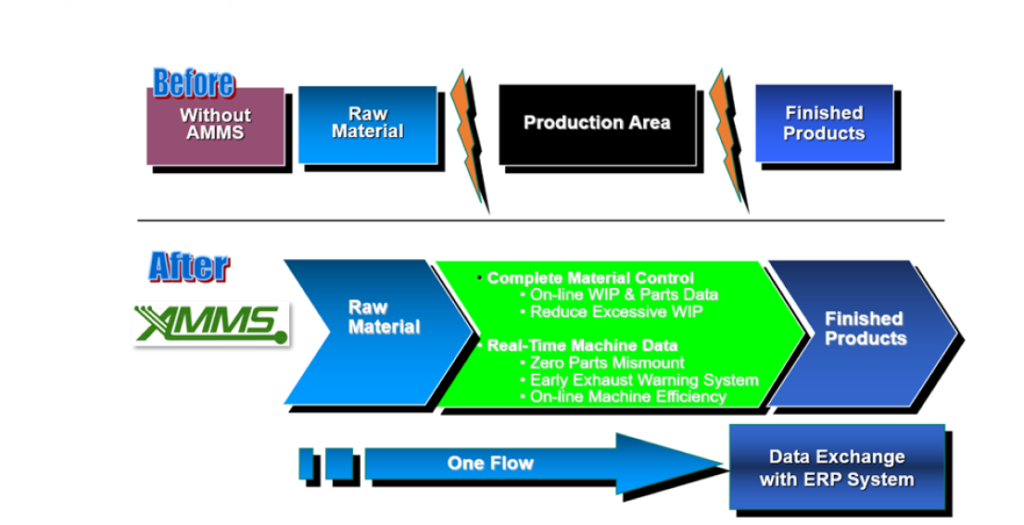